Egedal Maskinfabrik: Timegrip Gives Us Efficient Workflows
Egedal Maskinfabrik in Tørring, Central Jutland, has optimised their time tracking, project management, and cost calculations with Timegrip since the beginning of 2024. The result has been a more efficient workday, accurate data, and a system that adds value for both management and employees.
The company's 20 employees are blacksmiths, machinists, and fitters, who together have evolved into a global supplier of machinery for nurseries and forestry.
The Danish-owned company was established in 1934. Ninety years later, Egedal Maskinfabrik has successfully elevated their daily operations, with Timegrip lending a helping hand.
“We are very satisfied with the system we have in our hands,” says Mikkel Otte, Production Manager at Egedal Maskinfabrik.
A Time Tracking System at the Highest Level
Digitalising time tracking and employee scheduling is not new to Egedal Maskinfabrik. Previously, time tracking was a mix of paper forms and a digital punch clock system, which employees rarely used. This led to uncleat calculations and unnecessary time consumption, something that needed to change.
Mikkel Otte and the company's new Managing Director, Allan Koed Pedersen, scoured the internet for employee scheduling software.
“We needed something new that could be built from the ground up, and then we found your solution for time tracking, staffing and scheduling and thought it looked very interesting,” says Mikkel Otte.
One of the most crucial elements for a production company like Egedal Maskinfabrik is the ability for employees to clock in on specific production numbers. This significantly improves Mikkel Otte's overview of projects and costs.
“We got the employees to clock in on production numbers and enter the times into our punch clock software. With precise time tracking, we can continuously calculate costs for what we do and what we earn from it,” says Mikkel Otte.
Mikkel Otte, Production Manager, Egedal Maskinfabrik
Designed Specifically for Each Business
With Timegrip’s system integration options, Egedal Maskinfabrik has streamlined the entire process of project creation and subsequent cost calculations. The accurate data has fostered great confidence in the employee scheduling software and ensured the reliability of the figures the company works with.
“We have a ‘Pull from Timegrip’ button in our ERP system. It’s invaluable to be able to set up all the day’s tasks, press one button, and have everything transferred to your system, so staff can clock in on them. And it works the other way around too, from Timegrip to our ERP system,” says Mikkel Otte, emphasising his satisfaction with optimising time spent on cost calculations, shiftplanning and project registrations.
Since implementing Timegrip, there has been increased enthusiasm among employees, who have diverse preferences regarding working hours and shiftplanning. With the staff scheduling app, Mikkel Otte has an overview of when his staff are at work, giving the company the flexibility to allow employees to choose their own working hours.
“Employees have fairly free rein regarding when they clock in. As long as they complete 37 hours, they can more or less do as they like,” says Mikkel Otte, highlighting that Egedal Maskinfabrik also uses the Timegrip app for internal communication, allowing him to track when employees request time off, compensatory time, or have worked overtime.
Data from Timegrip Optimises Efficiency
Before implementing Timegrip, Egedal Maskinfabrik's project time tracking was based on ERP estimates. However, with Timegrip’s precise data calculations, the company has optimised daily efficiency and employee scheduling.
“With Timegrip, we can see that some of the old time estimates were way off. Now we can adjust the times on our production, so we are fully aware of the capacity we are working with. It’s invaluable for me to know how many orders we can handle,” says Mikkel Otte.
It’s not just on the production floor that Egedal Maskinfabrik has optimised workflows and gained an overview of projects and potential capacity. Even in the director’s office, the company has streamlined tasks and simplified payroll calculations.
“Our director handles payroll himself, and before, he would spend several hours processing wages. Now it takes just fifteen minutes. He saves an enormous amount of time on administrative work,” says Mikkel Otte.
Read how Franzefoss Minerals uses Timegrip for staff scheduling.
Support at the Forefront
“The great thing about Timegrip’s customer service is that if you have a question or something isn’t working, you just call, and it’s resolved within five minutes,” says Mikkel Otte.
“We were a bit apprehensive about moving to a 100% digital employee scheduling software because it can be challenging for some employees. But there has been nothing but positive feedback here. It’s been hugely beneficial to know that we’re never left to fend for ourselves because you’re so good at helping,” says Mikkel Otte, adding: “And overall, the system is just simple to navigate.”
With top-notch support, Egedal Maskinfabrik maximises the potential of the functions that Timegrip offers. Additionally, they play an active role in designing the functions in the employee scheduling software that are essential to their specific industry.
A Significant Change in Daily Operations
The shift from a mix of analogue paperwork and a digital punch clock system to a Workforce Management System like Timegrip has made the workdays easier for Egedal Maskinfabrik. This applies not only to production staff but also to those behind the desks, including Mikkel Otte and Allan Koed Pedersen. The handling of daily tasks, time tracking, staffing and scheduling is now smooth and streamlined for the traditional company, which continues to become more innovative under new ownership and the direction of Allan Koed Pedersen.
“We are truly happy with the system, and our employees appreciate how easy it is to use,” concludes Mikkel Otte.
Would you like to increase efficiency and have confidence in your data, time tracking and shiftplanning? Contact us today for a no-obligation consultation.
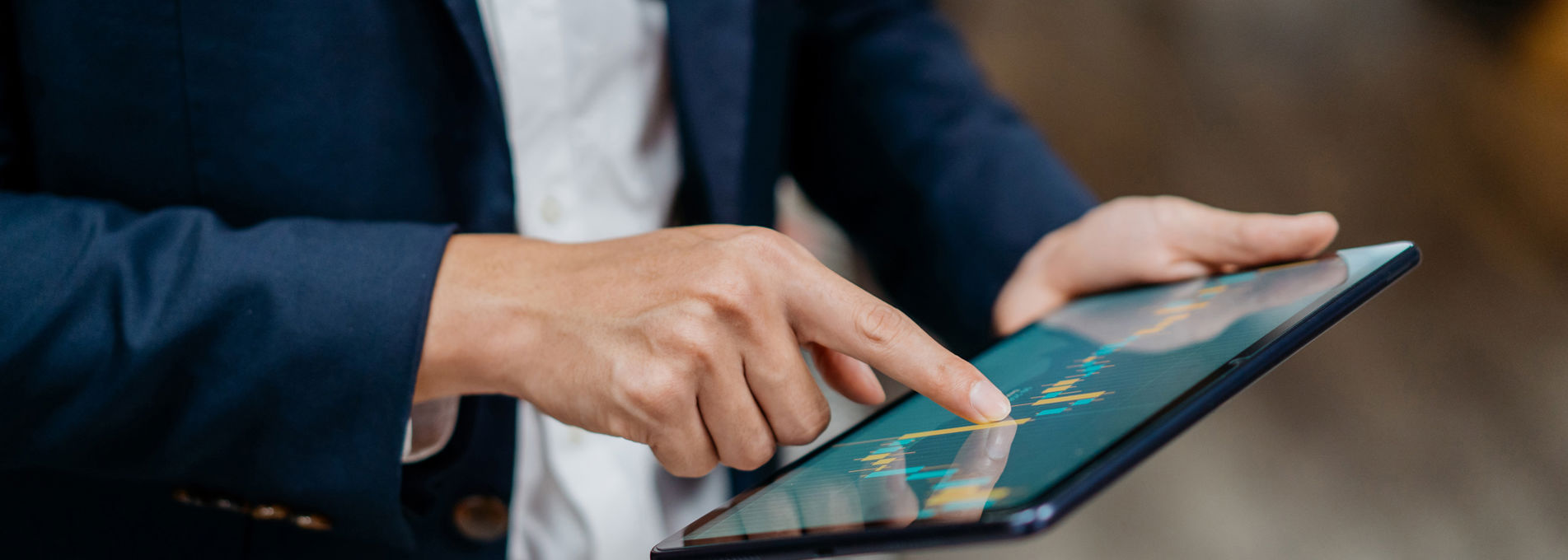